Understanding Nitinol melt
We offer fully integrated Nitinol melting production from ingot to finished product. Our independent melt is designed to support consistency in chemistry, microstructure, and performance that meets or exceeds ASTM standards. With both Plasma Arc Melting (PAM) and Vacuum Arc Remelting (VAR) in-house, we produce high-purity Nitinol tailored to demanding shape memory and superelastic applications.
From early innovation to high-volume production, we can support programs at any stage, while investments in additional equipment are expanding our scale to meet growing the demand for a secure Nitinol supply chain.
Contact us about melt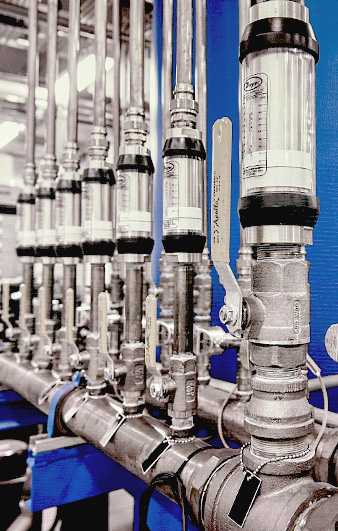
Our Nitinol melt options
Two generations of melt are available to align with a range of performance requirements. From standard applications to those requiring exceptional fatigue life, each grade is engineered to meet specific device and component demands.
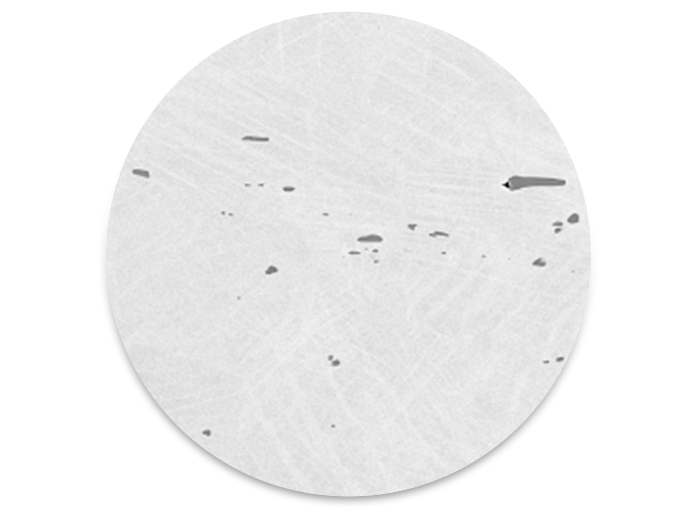
GEN I - Standard F2063
39 μm max. inclusion size
Ideal for our customers' standard stents, along with industrial actuators or couplings, and a number of additional med and non-med applications.
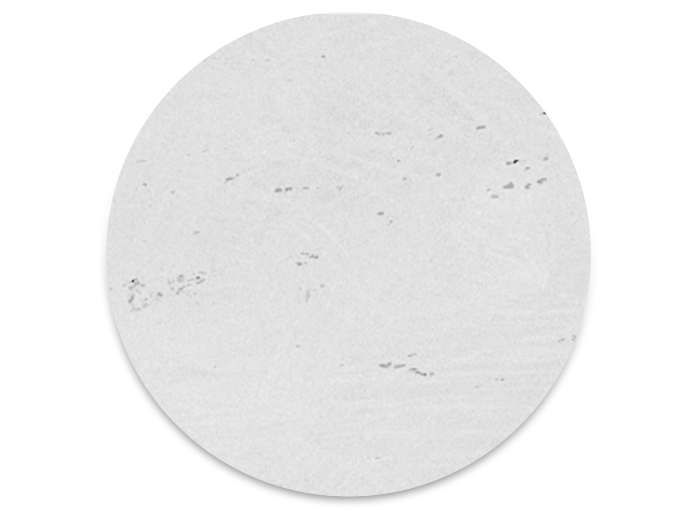
GEN II - Altus™ Nitinol
20 μm max. inclusion size
Additionally supports the demands of our customers' neurovascular stents and non-med applications including robotic flexures or precision instrumentation.
Nitinol melt, capabilities and product forms
A strong foundation in melt technology enables a wide variety of material forms and performance needs. We support a wide Nitinol product size range—from 0.0127 mm [0.0005 in] to 51 mm [2.00787 in]—to meet diverse application needs. Advanced micro-cleanliness and rigorous process validation help ensure consistent material quality.
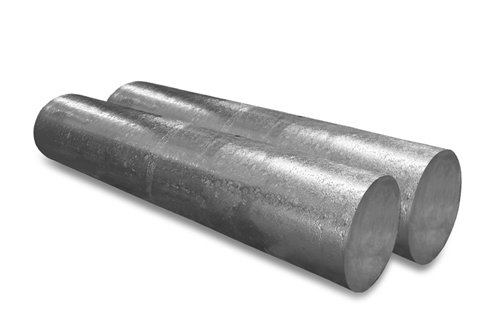
Product forms
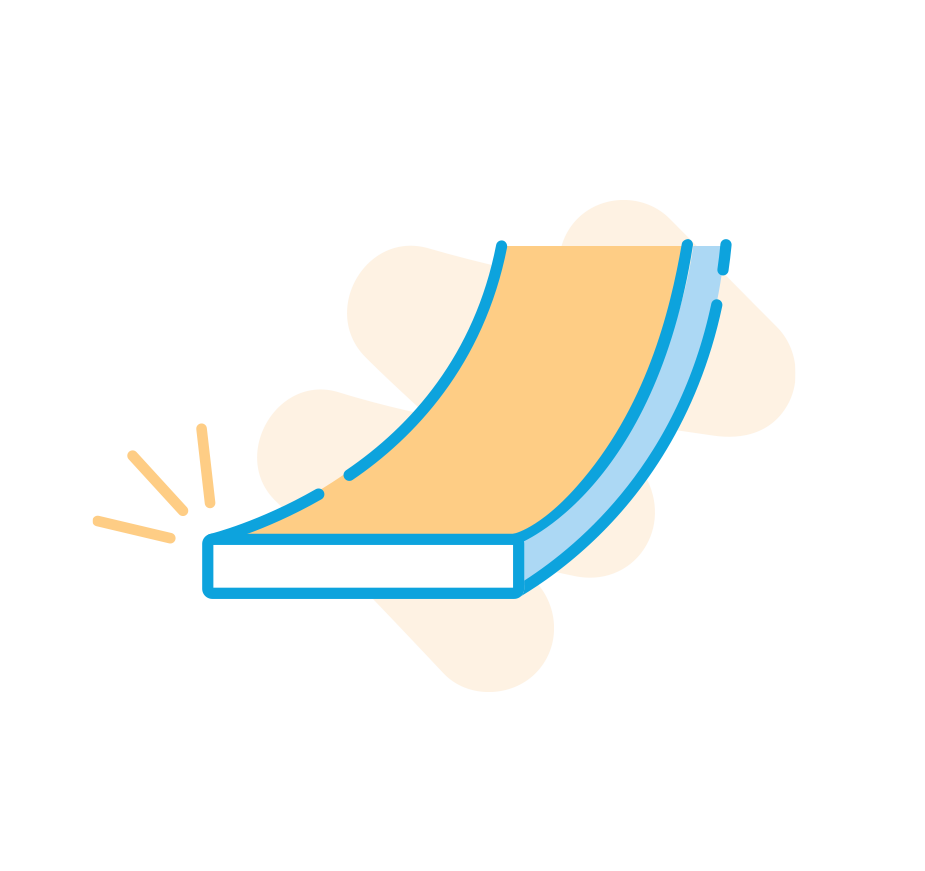
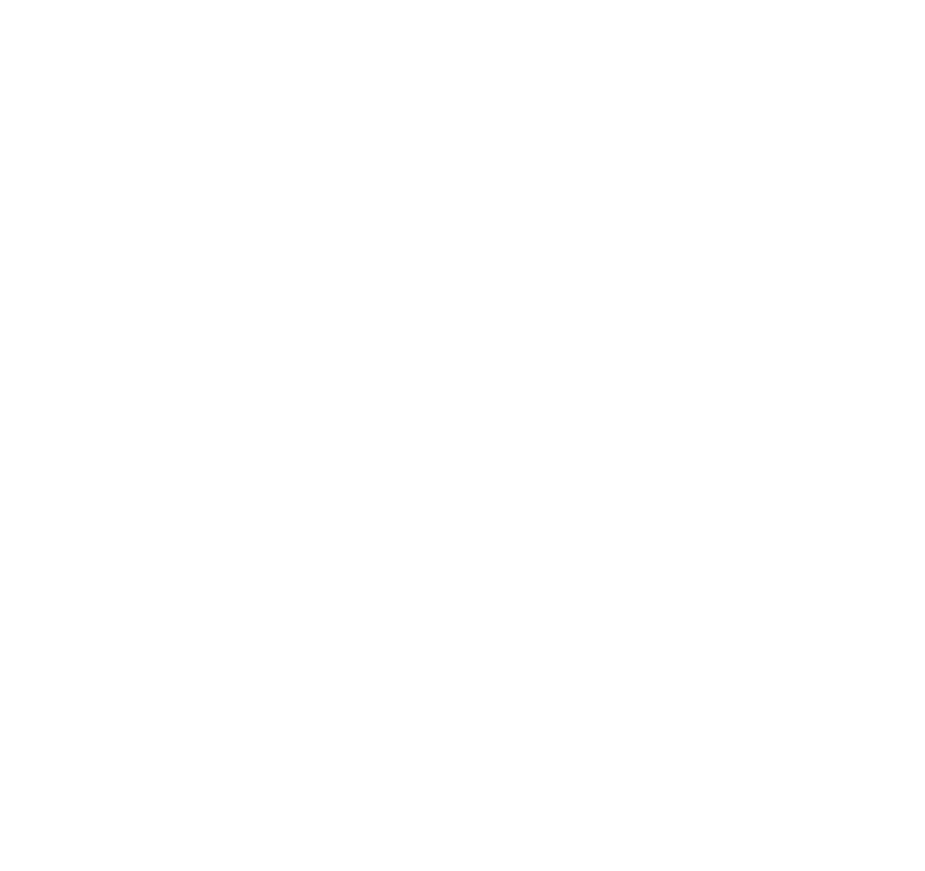
Strip
Rolled flat Nitinol with superelastic or shape memory properties.
Additional capabilities
From custom ingot melts to prototype wire and bar, our R&D team enables early-stage development with responsive expertise and flexible capabilities.
Whether you're testing new material or scaling up a concept, we're here to help move your ideas forward.
Our R&D team supports:
- Custom alloy development with various melt modalities
- Open capacity for custom projects
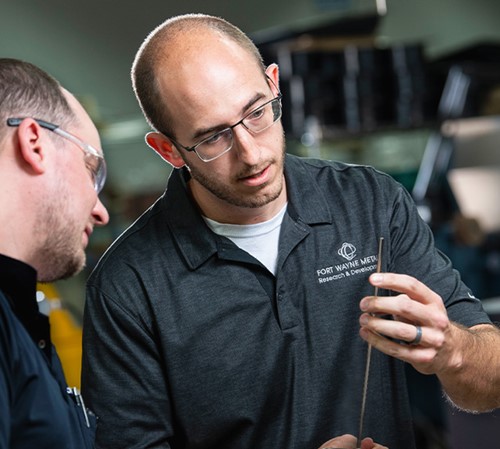
Candidate alloy families and materials offered:
- Aluminum
- Cobalt
- Cobalt-Chromium
- Iron
- Magnesium
- Nickel
- Nitinol
- Superelastic
- Shape memory
- Stainless Steel
- Titanium
- Zinc
If you don't see your desired material on the list, connect with our materials experts.
Our in-house Lab Services team plays a critical role in supporting melt quality and consistency. We offer a range of analytical tests to verify chemistry, inclusion control, and microstructure at every stage. These capabilities help validate process performance and support both R&D and production melts. With lab services integrated on-site, we maintain tighter feedback loops and faster response times.
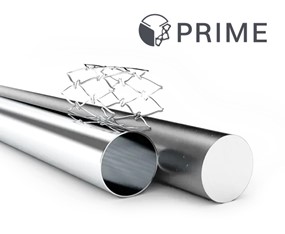
PRIME Project
PRIME: A joint initiative from ingot to implant.
We're proud to be part of PRIME (PRoficient Ingot Material Evaluation) — a strategic initiative uniting five trusted experts across the Nitinol supply chain. As the melting partner in this collaboration, we play a critical role in setting the foundation for consistent quality, reliable availability, and high-performance Nitinol.





Unable to load the form? Click the button below: